FORGED PIPE FITTINGS, FORGED TUBE FITTINGS, FORGED ELBOW, FORGED FITTINGS MANUFACTURERS, FORGED TEE, STAINLESS STEEL FORGED FITTINGS , FORGED COUPLING FITTINGS ,MS FORGED FITTINGS ,FORGED REDUCER ,ASME B16.11 FORGED FITTINGS, BUTT WELDINGS , HEX FORGED FITTINGS ,FORGED PIPE CONNECTIONS, CARBON STEEL FORGED PIPE FITTINGS, FORGED PIPE CAP
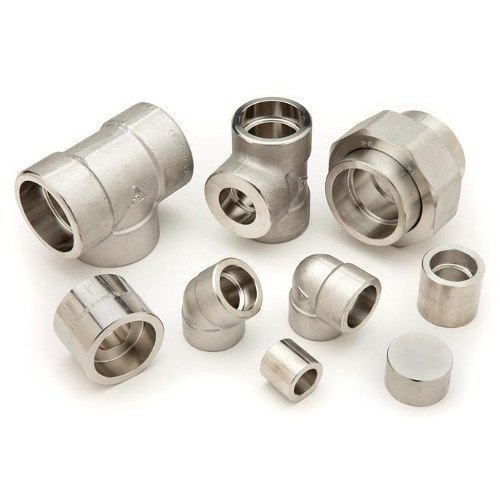
Forged pipe fittings are used for connecting nominal bore pipes.These fittings are available in sizes ranging from 1/8" to 4".Due to the forging-based manufacturing method, these fittings have their own name. When making these fittings, the raw material, which is an alloy of steel or carbon, is heated and shaped into a variety of shapes. These pipe fittings are constructed of nickel alloy, stainless steel, and A105 carbon steel. All of these basic materials are effective in creating pipe fittings. Forged pipe fittings are thicker, heavier, and designed for use in more demanding applications. The pressure classes indicated by these pipe fittings are 2000#, 3000#, 6000#, and 9000#.
Our Forged Fittings includes:
Types of Forged Fittings
Forged fittings come in a variety of types, each designed to serve a specific purpose. The most common types include elbows, tees, couplings, unions, and caps. Elbows are used to change the direction of the pipe, while tees allow for a branch connection. Couplings are used to connect two pipes together, and unions provide a convenient way to disassemble and reassemble pipes. Caps, on the other hand, are used to seal the end of a pipe. These different types of forged fittings offer versatility and enable efficient plumbing and pipeline systems in various industries.
When it comes to elbows, there are two main types: socket weld and threaded. Socket weld elbows have a female socket on one end and a male socket on the other, allowing for easy and secure connections. Threaded elbows, on the other hand, have male threads on both ends, which can be screwed into female-threaded pipes or fittings. Tees, couplings, unions, and caps also come in socket weld and threaded variations, providing flexibility in terms of installation options.
In addition to the standard types mentioned above, there are also specialized forged fittings available for specific applications. These include reducing tees, which allow for connections of different pipe sizes, and swage nipples, which are used to connect pipes of different diameters. It's important to consider the specific requirements of your project when choosing the right type of forged fitting.
Advantages of Using Forged Fittings
Forged fittings offer several advantages over other types of fittings, making them a popular choice in many industries. One of the main advantages is their superior strength and durability. The forging process involves shaping the fittings by applying compressive forces, resulting in a denser and stronger material compared to cast fittings. This makes forged fittings highly resistant to pressure, temperature, and corrosion, ensuring long-lasting performance even in demanding environments.
Another advantage of using forged fittings is their excellent dimensional accuracy. The forging process allows for precise shaping and sizing of the fittings, ensuring a tight and secure fit. This is crucial in plumbing and pipeline systems, as any gaps or misalignments can lead to leaks or failures. With forged fittings, you can have confidence in the integrity of your system, minimizing the risk of costly repairs or disruptions.
Furthermore, forged fittings offer improved flow characteristics compared to other types of fittings. The smooth interior surface of forged fittings reduces friction and turbulence, allowing for efficient fluid flow and minimizing pressure loss. This is particularly important in industries where the flow rate and efficiency are critical, such as oil and gas, chemical processing, and power generation.
Materials Used in Forged Fittings
Forged fittings can be made from a variety of materials, depending on the specific requirements of the application. The most commonly used materials include carbon steel, stainless steel, and alloy steel. Each material has its own unique properties and benefits, making them suitable for different environments and conditions.
Carbon steel forged fittings are the most widely used due to their affordability and excellent strength. They are suitable for a wide range of applications, including low-temperature services and high-pressure systems. Carbon steel fittings are also available in different grades, such as ASTM A105, ASTM A350 LF2, and ASTM A694 F52, each offering varying levels of tensile strength and impact resistance.
Stainless steel forged fittings, on the other hand, are highly corrosion-resistant and are often used in industries where hygiene and cleanliness are critical, such as food and beverage, pharmaceutical, and chemical processing. Stainless steel fittings are available in different grades, such as ASTM A182 F304, ASTM A182 F316, and ASTM A182 F321, each offering specific corrosion resistance properties.
Alloy steel forged fittings combine the strength of carbon steel with the corrosion resistance of stainless steel, making them suitable for high-temperature and high-pressure applications. Alloy steel fittings are commonly used in industries such as oil and gas, petrochemical, and power generation. Some common alloy steel grades used in forged fittings include ASTM A182 F5, ASTM A182 F9, and ASTM A182 F11.
When choosing the material for your forged fittings, it's important to consider factors such as the operating conditions, fluid compatibility, and regulatory requirements. Consulting with a knowledgeable supplier or engineer can help you make the right material selection for your specific application.
Manufacturing Process of Forged Fittings
The manufacturing process of forged fittings involves several steps, each contributing to the final product's strength, durability, and dimensional accuracy. The process begins with the selection of high-quality raw materials, such as billets or bars of the desired material grade. These raw materials are carefully inspected for defects or impurities that could compromise the quality of the final product.
Once the raw materials are approved, they are heated to a specific temperature to make them more malleable for forging. The heated billets or bars are then shaped into the desired forged fitting using one of three common forging methods: open die forging, closed die forging, or seamless rolled ring forging. Open die forging involves shaping the heated material between two flat dies, allowing for a wide range of shapes and sizes. Closed die forging, on the other hand, uses shaped dies to create a specific form or pattern. This method provides greater control over the final shape and size of the forged fitting.
Seamless rolled ring forging involves shaping the heated material into a ring shape by rolling it between two dies. This method is commonly used for larger forged fittings or when a seamless structure is required.
After the forging process, the forged fittings undergo heat treatment to enhance their mechanical properties and relieve any internal stresses. This involves heating the fittings to a specific temperature and then cooling them slowly to ensure optimal strength and toughness. The heat treatment process is crucial in achieving the desired mechanical properties and ensuring the integrity of the forged fittings.
Once the heat treatment is complete, the forged fittings undergo machining and finishing processes to achieve the final dimensions and surface quality. This may involve cutting, drilling, threading, or polishing, depending on the specific requirements of the fitting. The finished forged fittings are then thoroughly inspected for quality assurance before being packaged and shipped to customers.
Common Applications of Forged Fittings
Forged fittings have a wide range of applications across various industries, thanks to their strength, durability, and versatility. Some common applications include oil and gas pipelines, chemical processing plants, power generation facilities, petrochemical refineries, and shipbuilding.
vv
In oil and gas pipelines, forged fittings are used to connect and control the flow of oil, gas, and other fluids. Their high-pressure and corrosion-resistant properties make them ideal for withstanding the harsh conditions encountered in the oil and gas industry.
Chemical processing plants often rely on forged fittings for their resistance to corrosive chemicals and high-temperature environments. These fittings ensure the safe and efficient transportation of various chemicals and fluids throughout the plant.
Power generation facilities, such as thermal power plants and nuclear power plants, use forged fittings in their piping systems to handle high-pressure steam and other fluids. The strength and reliability of forged fittings are crucial in maintaining the safety and efficiency of these critical systems.
Petrochemical refineries require forged fittings for their ability to handle a wide range of chemicals, including corrosive and volatile substances. These fittings play a vital role in maintaining the integrity of the piping systems and preventing leaks or failures that could result in accidents or environmental hazards.
Shipbuilding industry relies on forged fittings for their strength and durability in marine environments. These fittings are used in various applications, including piping systems, engine components, and structural supports, ensuring the safety and reliability of marine vessels.
Choosing the Right Forged Fittings for Your Project
Choosing the right forged fittings for your project requires careful consideration of several factors, including the operating conditions, fluid characteristics, and system requirements. Here are some key factors to keep in mind when selecting forged fittings
Material
Consider the specific requirements of your project and choose the appropriate material grade. Carbon steel, stainless steel, and alloy steel each offer unique properties and benefits, so it's important to select the material that best suits your application.
Pressure and Temperature Rating
Ensure that the forged fittings you choose can handle the maximum pressure and temperature conditions of your system. Refer to industry standards and specifications for guidance on pressure and temperature ratings.
Corrosion Resistance
If your project involves corrosive fluids or environments, it's important to select forged fittings with excellent corrosion resistance properties. Stainless steel or alloy steel fittings may be more suitable for such applications.
Size and Dimensions
Consider the size and dimensions of the pipes or fittings you need to connect. Ensure that the forged fittings are compatible with the pipe sizes and have the necessary dimensions for a proper fit.
Quality and Certification
Look for forged fittings that meet industry quality standards and have appropriate certifications, such as ASTM, ASME, or API. This ensures that the fittings have been tested and approved for use in specific applications.
Comparison between Forged Fittings and Other Types of Fittings
While forged fittings offer numerous advantages, it's important to consider the specific requirements of your project and compare them with other types of fittings to make an informed decision. Here are some key points of comparison
Strength and Durability
Forged fittings are known for their superior strength and durability compared to cast fittings, which may be more prone to defects or failures. If your project involves high-pressure or high-temperature conditions, forged fittings may offer better reliability and safety.
Corrosion Resistance
Stainless steel or alloy steel forged fittings offer excellent corrosion resistance, making them suitable for applications involving corrosive fluids or environments. Cast fittings may have lower corrosion resistance, requiring additional protective measures.
Cost
Forged fittings are generally more expensive than cast fittings due to the complexity of the manufacturing process and the higher quality of the final product. However, the long-term benefits and performance of forged fittings may outweigh the initial cost.
Availability
Cast fittings are more readily available and can be found in a wider range of sizes and configurations compared to forged fittings. If your project requires specific dimensions or specialized fittings, forged fittings may be more suitable, albeit with potentially longer lead times.
Customization
Forged fittings can be customized to meet specific project requirements, such as unique shapes, sizes, or materials. This flexibility allows for tailored solutions, especially in complex or specialized applications.
Countries we export to: Forged Pipe Fittings Manufacturers / Suppliers / Stockist in Kuwait, Forged Pipe Fittings Manufacturers in UAE, Forged Pipe Fittings Manufacturers in Germany, Forged Pipe Fittings Manufacturers in Saudi Arabia, Forged Pipe Fittings Manufacturers in West Africa, Forged Pipe Fittings Manufacturers in Iraq, Forged Pipe Fittings Manufacturers in Congo, Forged Pipe Fittings Manufacturers in Mexico, Forged Pipe Fittings Manufacturers in Bahrain, Forged Pipe Fittings Manufacturers in Canada, Forged Pipe Fittings Manufacturers in Philippines, Forged Pipe Fittings Manufacturers in Thailand, Forged Pipe Fittings Manufacturers in Kenya, Forged Pipe Fittings Manufacturers in Oman, Forged Pipe Fittings Manufacturers in Malaysia, Forged Pipe Fittings Manufacturers in Turkey, Forged Pipe Fittings Manufacturers in Qatar, Forged Pipe Fittings Manufacturers in Sudan, Forged Pipe Fittings Manufacturers in Netherlands, Forged Pipe Fittings Manufacturers in Oman, Forged Pipe Fittings Manufacturers in Nigeria, Forged Pipe Fittings Manufacturers in Lithuania, Forged Pipe Fittings Manufacturers in Gabon, Forged Pipe Fittings Manufacturers in Russia, Forged Pipe Fittings Manufacturers in Vietnam, Forged Pipe Fittings Manufacturers in Angola, Forged Pipe Fittings Manufacturers in Bolivia, Forged Pipe Fittings Manufacturers in Indonesia, Forged Pipe Fittings Manufacturers in UK, Forged Pipe Fittings Manufacturers in Yemen, Forged Pipe Fittings Manufacturers in Italy, Forged Pipe Fittings Manufacturers in United States, Forged Pipe Fittings Manufacturers in Venezuela, Forged Pipe Fittings Manufacturers in Spain, Forged Pipe Fittings Manufacturers in Iran, Forged Pipe Fittings Manufacturers in Estonia, Forged Pipe Fittings Manufacturers in Kazakhstan, Forged Pipe Fittings Manufacturers in Algeria, Forged Pipe Fittings Manufacturers in Jordan, Forged Pipe Fittings Manufacturers in Ecuador, Forged Pipe Fittings Manufacturers in Portugal, Forged Pipe Fittings Manufacturers in Colombia, Forged Pipe Fittings Manufacturers in Libya, Forged Pipe Fittings Manufacturers in Chile, Forged Pipe Fittings Manufacturers in Peru, Forged Pipe Fittings Manufacturers in Iran, Forged Pipe Fittings Manufacturers in South Africa, Forged Pipe Fittings Manufacturers in Bangkok, Forged Pipe Fittings Manufacturers in Namibia, Forged Pipe Fittings Manufacturers in Jeddah, Forged Pipe Fittings Manufacturers in Afghanistan, Forged Pipe Fittings Manufacturers in Israel, Forged Pipe Fittings Manufacturers in Zambia, Forged Pipe Fittings Manufacturers in Macau, Forged Pipe Fittings Manufacturers in Morocco, Forged Pipe Fittings Manufacturers in Denmark, Forged Pipe Fittings Manufacturers in Taiwan, Forged Pipe Fittings Manufacturers in Norway, Forged Pipe Fittings Manufacturers in Belarus, Forged Pipe Fittings Manufacturers in North Macedonia, Forged Pipe Fittings Manufacturers in Lebanon, Forged Pipe Fittings Manufacturers in Sri Lanka, Forged Pipe Fittings Manufacturers in Bhutan, Forged Pipe Fittings Manufacturers in Bulgaria, Forged Pipe Fittings Manufacturers in Albania, Forged Pipe Fittings Manufacturers in Ukraine, Forged Pipe Fittings Manufacturers in Belgium, Forged Pipe Fittings Manufacturers in Finland, Forged Pipe Fittings Manufacturers in Slovokia, Forged Pipe Fittings Manufacturers in Tibet, Forged Pipe Fittings Manufacturers in Romania, Forged Pipe Fittings Manufacturers in France, Forged Pipe Fittings Manufacturers in Brazil, Forged Pipe Fittings Manufacturers in Trinidad & Tobago, Forged Pipe Fittings Manufacturers in Fiji, Forged Pipe Fittings Manufacturers in Tunisia, Forged Pipe Fittings Manufacturers in Gambia, Forged Pipe Fittings Manufacturers in Mexico, Forged Pipe Fittings Manufacturers in Hungary, Forged Pipe Fittings Manufacturers in Zimbabwe, Forged Pipe Fittings Manufacturers in Mongolia, Forged Pipe Fittings Manufacturers in Ghana, Forged Pipe Fittings Manufacturers in Egypt, Forged Pipe Fittings Manufacturers in Kazakhstan, Forged Pipe Fittings Manufacturers in Czech Republic, Forged Pipe Fittings Manufacturers in Azerbaijan, Forged Pipe Fittings Manufacturers in Poland, Forged Pipe Fittings Manufacturers in Greece, Forged Pipe Fittings Manufacturers in Costa Rica, Forged Pipe Fittings Manufacturers in Kosovo, Forged Pipe Fittings Manufacturers in New Zealand, Forged Pipe Fittings Manufacturers in Croatia, Forged Pipe Fittings Manufacturers in Puerto Rico, Forged Pipe Fittings Manufacturers in Tanzania, Forged Pipe Fittings Manufacturers in Somalia.
Major Exporting Areas: Forged Pipe Fittings Manufacturers / Suppliers / Stockist in Moscow, Port-Of-Spain, Seoul, Montreal, Dubai, Kuala Lumpur, Aberdeen, Tehran, Bogota, Petaling Jaya, Melbourne, Abu Dhabi, Courbevoie, Edmonton, Ho Chi Minh City, Bangkok, Toronto, Muscat, Milan, Busan, Mexico City, Perth, La Victoria, Santiago, Rio de Janeiro, London, Karachi, Los Angeles, Manama, Geoje-si, Atyrau, Sydney, Riyadh, New York, Jeddah, Houston, Granada, Jakarta, Brisbane, Algiers, Kuwait City, Dubai, Hanoi, Doha, Al Jubail, Chiyoda, Cairo, Gimhae-si, Caracas, Lagos, Al Khobar, Madrid, Singapore, Calgary, Colombo, Ulsan, Istanbul, Ahvaz, Dammam, Dallas, Texas, Ankara, Sharjah, Vung Tau, Angola, Benin, Burundi, Botswana, Burkina Faso, Cameroon, Douala, Central African Republic, Republic of Congo, Democratic Republic of Congo, Côte d'Ivoire, Djibouti, Eritrea, Ethiopia, Equatorial Guinea, Gabon, Guinea, Kenya, Liberia,Malawi, Mali, Mauritania, Mauritius, Casablanca-Settat, Tanger-Tetouan-Al Hoceima, Fès-Meknès, Marrakesh-Safi, Oriental, Béni Mellal-Khénifra, Souss-Massa, Laâyoune-Sakia El Hamra, Rabat-Salé-Kénitra region, Mozambique, Temara, Niger, Rwanda, Senegal, Sierra Leone, Sudan, Tanzania, Togo, Uganda, Bangkok, Bangchan, Khlong Sam Wa, Gemopolis, Lard Krabang, Pathumthani, Bangkadi, Navanakorn, Samut Prakarn, Bangplee, Bangpoo, Saraburi, Nongkhae, SIL I/Land, Chachoengsao, Alloy 20 I/P, Gateway City, Wellgrow, Rayong, Amata City, Eastern Seaboard, Hemaraj Eastern Seaboard, Rojana, Soam Eastern, Chonburi, Amata Nakorn, Hemaraj Chonburi, Pinthong, Ayutthaya, Bangpa-in, Saha Ratna Nakorn, Nakornratchasima, Kabinburi, Prachinburi, HCMC, Tan Thuan Export Processing Zone, Bien Hoa, Dong Nai Province, Amata City Bien Hoa Industrial Park, Long Binh Techno Park, Binh Duong Province, Vietnam Singapore Industrial Park, My Phuoc Industrial Park, Ho Nai Industrial Zone, Bau Xeo Industrial Park, Long Thanh Industrial Zone, Long Duc Industrial Park, Duc Hao I, Tan Huong, Long Jiang, Tra Noc I/II, Hung Phu I, Hiep Phuoc Industrial Park, Phuoc Dong Industrial Park, Dinh Vu – Cat Hai Economic Zone.
SPECIFICATIONS
STAINLESS STEEL: 310, 304, 304H, 304L, 316, 316L, 321, RA330
INCONEL: 600, 601, 602CA, 625, 690, 800, 800H, 800HT
MONEL: 400, K500
HASTELLOY: C276, C22
253MA
3mm - 18mm
CUSTOMIZED