Hex Mesh Manufacturer, Honeycombed Steel Manufacturer, Honeycomb steel Manufacturer, Mesh Hex Manufacturer, Refractory Mesh, Hex Refractory
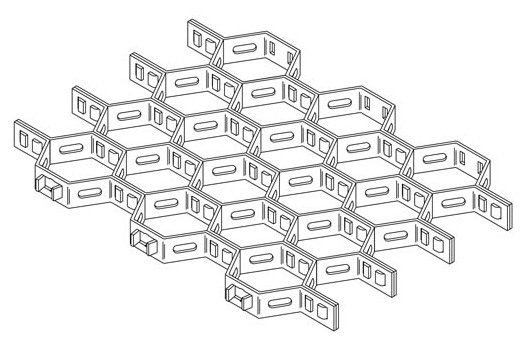
Hex Mesh is a honeycombed steel for installation in refractories. Hex Mesh provides excellent reinforcement and retention to thin wall refractories. It fully complements dense hydraulic and chemically bonded refractories in resisting erosion.
Dimensions of Hex Mesh
The dimensions of hex mesh are according to METALX standard part numbers or customer specifications / drawing. METALX ENGINEERING INC is capable of manufacturing all types of hex mesh with precise dimensions.
How does hex mesh refractory work?
Hex mesh refractory is a unique material that combines the strength and durability of refractory bricks with the flexibility and adaptability of mesh. The hexagonal mesh structure consists of interconnected wires, forming a three-dimensional honeycomb pattern. This structure provides excellent thermal shock resistance and allows for efficient heat transfer, making it ideal for high-temperature applications.
One of the key characteristics of hex mesh refractory is its ability to trap and contain heat within its structure. The hexagonal shape of the mesh creates small pockets of air, which act as insulating barriers. This insulation helps to minimize heat loss and ensures that the surrounding environment remains at a safe temperature. Additionally, the mesh structure allows for the expansion and contraction of the refractory material, reducing the risk of cracking and failure under extreme thermal conditions.
Hex mesh refractory also offers superior erosion and corrosion resistance. The interlocking wires create a strong and robust barrier that can withstand the harsh conditions found in many industrial processes. This resistance to erosion and corrosion ensures the longevity and reliability of the refractory lining, saving both time and money on maintenance and replacement.
In summary, hex mesh refractory works by utilizing its unique hexagonal mesh structure to provide excellent insulation, heat transfer, thermal shock resistance, and erosion/corrosion resistance. This combination of properties makes it an ideal choice for a wide range of high-temperature applications.
Advantages of using hex mesh refractory
When it comes to high-temperature applications, hex mesh refractory offers several advantages over other refractory materials. Let's explore some of these benefits in detail:
Superior insulation
Hex mesh refractory provides exceptional insulation properties due to its honeycomb structure. It effectively traps heat within its structure, minimizing heat loss and maintaining a stable temperature in the surrounding environment. This insulation ability helps to reduce energy consumption and improve overall process efficiency.
Excellent thermal shock resistance
Hex mesh refractory is designed to withstand rapid changes in temperature without cracking or failing. The interlocking wires in the mesh structure allow for expansion and contraction, preventing thermal shock damage. This property is crucial in applications that involve frequent temperature fluctuations.
Outstanding erosion and corrosion resistance
Hex mesh refractory is highly resistant to erosion and corrosion caused by chemicals, gases, and molten materials. The robust mesh structure acts as a protective barrier, ensuring the longevity and performance of the refractory lining. This resistance results in reduced maintenance costs and increased operational reliability.
Versatile and customizable
Hex mesh refractory can be tailored to meet specific application requirements. The mesh size, wire diameter, and material composition can be adjusted to achieve desired thermal properties, mechanical strength, and chemical resistance. This versatility makes it suitable for a wide range of industries and processes.
Easy installation and maintenance
Hex mesh refractory is lightweight and flexible, making it easier to handle and install compared to traditional refractory bricks. The mesh structure can be easily cut and shaped to fit complex geometries, reducing installation time and effort. Additionally, the smooth surface of the mesh makes it easier to clean and maintain, further enhancing its usability.
Flexibility and adaptability
Hex mesh refractory is lightweight and flexible, making it easier to handle and install compared to solid bricks. The mesh structure can be cut and shaped to fit complex geometries, reducing installation time and effort.
Cost-effectiveness:
While the initial cost of hex mesh refractory may be slightly higher compared to traditional refractory materials, its long-term cost-effectiveness is evident. The superior insulation properties and durability of hex mesh refractory result in reduced energy consumption, maintenance costs, and downtime.
In conclusion, the advantages of hex mesh refractory, including superior insulation, thermal shock resistance, erosion/corrosion resistance, versatility, and ease of installation/maintenance, make it a preferred choice for many high-temperature applications.
Applications of hex mesh refractory
Hex mesh refractory finds extensive use in a variety of industries and applications where high temperatures, erosion, and corrosion are prevalent. Let's explore some of the key areas where hex mesh refractory excels:
Petrochemical industry
Hex mesh refractory is widely used in the petrochemical industry for applications such as reformers, ethylene crackers, and process heaters. The ability to withstand extreme temperatures and resist chemical attack makes it an ideal choice for lining furnaces, reactors, and other process equipment.
Steel industry
Hex mesh refractory is essential in steelmaking processes, including blast furnaces, hot metal transfer systems, and ladles. Its superior thermal shock resistance and erosion/corrosion resistance make it suitable for withstanding the harsh conditions found in steel production.
Cement industry
Hex mesh refractory is utilized in cement kilns and preheaters, where it provides excellent insulation and resistance to alkali attack. The ability to maintain high temperatures and withstand the corrosive nature of cement ensures the durability and efficiency of these critical components.
Incineration plants
Hex mesh refractory is commonly used in waste incineration plants to line the combustion chambers and flue gas ducts. Its high thermal shock resistance and erosion/corrosion resistance help to maintain optimal operating conditions and reduce the impact of harmful emissions.
Glass industry
Hex mesh refractory plays a vital role in glass manufacturing, particularly in glass melting furnaces. Its ability to withstand high temperatures and resist chemical attack from molten glass ensures the longevity and efficiency of the furnaces.
These are just a few examples of the many applications where hex mesh refractory is employed. Its unique combination of properties makes it a versatile and reliable choice for industries that require high-temperature insulation and protection.
Maintenance of hex mesh refractory
Proper maintenance are crucial to maintaining the performance and longevity of hex mesh refractory. Here are some essential tips to help you keep your refractory lining in optimal condition:
Regular inspections
Conduct regular visual inspections of the refractory lining to identify any signs of damage, erosion, or corrosion. Inspect for cracks, spalling, or areas of discoloration. Address any issues promptly to prevent further damage or performance degradation.
Repair and maintenance
Address any identified issues promptly through appropriate repairs or maintenance activities. This may involve patching or reapplying refractory material, sealing gaps, or replacing damaged sections. Follow the recommended repair procedures and consult with refractory experts if needed.
Thermal cycling
Avoid rapid temperature changes or thermal cycling, as this can stress the refractory lining and lead to cracking or failure. If thermal cycling is unavoidable, consider selecting refractory materials specifically designed for such conditions or explore insulation solutions to minimize thermal shock.
Chemical exposure
Be mindful of the chemical environment in which the hex mesh refractory is operating. Certain chemicals or gases may corrode or deteriorate the refractory material over time. Use appropriate chemical-resistant refractory materials or coatings to mitigate the effects of chemical exposure.
By following these tips, you can ensure the optimal performance and longevity of your hex mesh refractory. Regular inspections and timely repairs will help prevent costly downtime and ensure the efficiency of your high-temperature processes.
Also known as:
Countries we export to: Hex mesh Manufacturers / Suppliers / Stockist in Kuwait, Hex mesh Manufacturers in UAE, Hex mesh Manufacturers in Germany, Hex mesh Manufacturers in Saudi Arabia, Hex mesh Manufacturers in West Africa, Hex mesh Manufacturers in Iraq, Hex mesh Manufacturers in Congo, Hex mesh Manufacturers in Mexico, Hex mesh Manufacturers in Bahrain, Hex mesh Manufacturers in Canada, Hex mesh Manufacturers in Philippines, Hex mesh Manufacturers in Thailand, Hex mesh Manufacturers in Kenya, Hex mesh Manufacturers in Oman, Hex mesh Manufacturers in Malaysia, Hex mesh Manufacturers in Turkey, Hex mesh Manufacturers in Qatar, Hex mesh Manufacturers in Sudan, Hex mesh Manufacturers in Netherlands, Hex mesh Manufacturers in Oman, Hex mesh Manufacturers in Nigeria, Hex mesh Manufacturers in Lithuania, Hex mesh Manufacturers in Gabon, Hex mesh Manufacturers in Russia, Hex mesh Manufacturers in Vietnam, Hex mesh Manufacturers in Angola, Hex mesh Manufacturers in Bolivia, Hex mesh Manufacturers in Indonesia, Hex mesh Manufacturers in UK, Hex mesh Manufacturers in Yemen, Hex mesh Manufacturers in Italy, Hex mesh Manufacturers in United States, Hex mesh Manufacturers in Venezuela, Hex mesh Manufacturers in Spain, Hex mesh Manufacturers in Iran, Hex mesh Manufacturers in Estonia, Hex mesh Manufacturers in Kazakhstan, Hex mesh Manufacturers in Algeria, Hex mesh Manufacturers in Jordan, Hex mesh Manufacturers in Ecuador, Hex mesh Manufacturers in Portugal, Hex mesh Manufacturers in Colombia, Hex mesh Manufacturers in Libya, Hex mesh Manufacturers in Chile, Hex mesh Manufacturers in Peru, Hex mesh Manufacturers in Iran, Hex mesh Manufacturers in South Africa, Hex mesh Manufacturers in Bangkok, Hex mesh Manufacturers in Namibia, Hex mesh Manufacturers in Jeddah, Hex mesh Manufacturers in Afghanistan, Hex mesh Manufacturers in Israel, Hex mesh Manufacturers in Zambia, Hex mesh Manufacturers in Macau, Hex mesh Manufacturers in Morocco, Hex mesh Manufacturers in Denmark, Hex mesh Manufacturers in Taiwan, Hex mesh Manufacturers in Norway, Hex mesh Manufacturers in Belarus, Hex mesh Manufacturers in North Macedonia, Hex mesh Manufacturers in Lebanon, Hex mesh Manufacturers in Sri Lanka, Hex mesh Manufacturers in Bhutan, Hex mesh Manufacturers in Bulgaria, Hex mesh Manufacturers in Albania, Hex mesh Manufacturers in Ukraine, Hex mesh Manufacturers in Belgium, Hex mesh Manufacturers in Finland, Hex mesh Manufacturers in Slovokia, Hex mesh Manufacturers in Tibet, Hex mesh Manufacturers in Romania, Hex mesh Manufacturers in France, Hex mesh Manufacturers in Brazil, Hex mesh Manufacturers in Trinidad & Tobago, Hex mesh Manufacturers in Fiji, Hex mesh Manufacturers in Tunisia, Hex mesh Manufacturers in Gambia, Hex mesh Manufacturers in Mexico, Hex mesh Manufacturers in Hungary, Hex mesh Manufacturers in Zimbabwe, Hex mesh Manufacturers in Mongolia, Hex mesh Manufacturers in Ghana, Hex mesh Manufacturers in Egypt, Hex mesh Manufacturers in Kazakhstan, Hex mesh Manufacturers in Czech Republic, Hex mesh Manufacturers in Azerbaijan, Hex mesh Manufacturers in Poland, Hex mesh Manufacturers in Greece, Hex mesh Manufacturers in Costa Rica, Hex mesh Manufacturers in Kosovo, Hex mesh Manufacturers in New Zealand, Hex mesh Manufacturers in Croatia, Hex mesh Manufacturers in Puerto Rico, Hex mesh Manufacturers in Tanzania, Hex mesh Manufacturers in Somalia.
Major Exporting Areas: Hex Mesh Manufacturers / Suppliers / Stockist in Moscow, Port-Of-Spain, Seoul, Montreal, Dubai, Kuala Lumpur, Aberdeen, Tehran, Bogota, Petaling Jaya, Melbourne, Abu Dhabi, Courbevoie, Edmonton, Ho Chi Minh City, Bangkok, Toronto, Muscat, Milan, Busan, Mexico City, Perth, La Victoria, Santiago, Rio de Janeiro, London, Karachi, Los Angeles, Manama, Geoje-si, Atyrau, Sydney, Riyadh, New York, Jeddah, Houston, Granada, Jakarta, Brisbane, Algiers, Kuwait City, Dubai, Hanoi, Doha, Al Jubail, Chiyoda, Cairo, Gimhae-si, Caracas, Lagos, Al Khobar, Madrid, Singapore, Calgary, Colombo, Ulsan, Istanbul, Ahvaz, Dammam, Dallas, Texas, Ankara, Sharjah, Vung Tau, Angola, Benin, Burundi, Botswana, Burkina Faso, Cameroon, Douala, Central African Republic, Republic of Congo, Democratic Republic of Congo, Côte d'Ivoire, Djibouti, Eritrea, Ethiopia, Equatorial Guinea, Gabon, Guinea, Kenya, Liberia,Malawi, Mali, Mauritania, Mauritius, Casablanca-Settat, Tanger-Tetouan-Al Hoceima, Fès-Meknès, Marrakesh-Safi, Oriental, Béni Mellal-Khénifra, Souss-Massa, Laâyoune-Sakia El Hamra, Rabat-Salé-Kénitra region, Mozambique, Temara, Niger, Rwanda, Senegal, Sierra Leone, Sudan, Tanzania, Togo, Uganda, Bangkok, Bangchan, Khlong Sam Wa, Gemopolis, Lard Krabang, Pathumthani, Bangkadi, Navanakorn, Samut Prakarn, Bangplee, Bangpoo, Saraburi, Nongkhae, SIL I/Land, Chachoengsao, Alloy 20 I/P, Gateway City, Wellgrow, Rayong, Amata City, Eastern Seaboard, Hemaraj Eastern Seaboard, Rojana, Soam Eastern, Chonburi, Amata Nakorn, Hemaraj Chonburi, Pinthong, Ayutthaya, Bangpa-in, Saha Ratna Nakorn, Nakornratchasima, Kabinburi, Prachinburi, HCMC, Tan Thuan Export Processing Zone, Bien Hoa, Dong Nai Province, Amata City Bien Hoa Industrial Park, Long Binh Techno Park, Binh Duong Province, Vietnam Singapore Industrial Park, My Phuoc Industrial Park, Ho Nai Industrial Zone, Bau Xeo Industrial Park, Long Thanh Industrial Zone, Long Duc Industrial Park, Duc Hao I, Tan Huong, Long Jiang, Tra Noc I/II, Hung Phu I, Hiep Phuoc Industrial Park, Phuoc Dong Industrial Park, Dinh Vu – Cat Hai Economic Zone.
SPECIFICATIONS
STAINLESS STEEL: 310, 304, 304H, 304L, 316, 316L, 321, RA330
INCONEL: 600, 601, 602CA, 625, 690, 800, 800H, 800HT
MONEL: 400, K500
HASTELLOY: C276, C22
253MA
- High temperature stability
- Aids erosion resistance
- Superior retention
- Protection of refractory materials